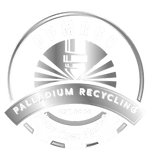
Platinum $1,986.85 Palladium $1,286.83 Rhodium $6550 Gold $2338.14
Incoporated and Operated Since 2005
Protect your wealth from the next recession
Two decades of Precious Metals Expertise. Lowest Prices, Guaranteed
Real-time pricing on precious metals. Invest now and reap the rewards.
Fast Shipping: Orders are usually processed and shipped within one business day
Catalytic Converter Compositions – Clearing the Air
PPMRCC Recycling
PPMRCC recycling focuses on recovering precious metals, especially platinum group metals (PGMs), from sources like catalytic converters, electronics, and jewelry. PGMs, comprising platinum, palladium, and rhodium, are highly prized for their unique properties and industrial uses.”
The Recycling Process:
-
Collection and Sorting: Catalytic converters, the primary source of PGMs, are collected from end-of-life vehicles. They are then sorted and processed to remove any non-PGM materials.
-
Processing: The catalytic converters are subjected to various processing techniques, such as crushing, grinding, and chemical treatment, to extract the precious metals.
-
Refining: The extracted PGMs are refined to purify them and separate them from other metals and impurities. This process often involves a combination of chemical and physical methods.
-
Forming and Packaging: The refined PGMs are formed into specific shapes or sizes, such as ingots or powders, and packaged for shipment to various industries.

-
Experience: PPMRCC has been in the catalytic converter scrap business since 2005.
-
Growth: The company has expanded from a specialized buyer to a leading information provider and toll-refining purchaser in South Africa.
-
Sustainability Focus: PPMRCC emphasizes the importance of sustainable precious metal recycling, particularly for platinum, palladium, and rhodium (PGMs) from catalytic converters.
Overall, PPMRCC is a well-established company in the catalytic converter recycling industry, committed to sustainable practices and extracting maximum value from precious metals.
The Importance of PGM Recycling: A Sustainable Future
Your introduction highlights the critical role of PGM recycling in promoting a sustainable future. Let's delve deeper into the reasons why:
1. Conservation of Natural Resources:
-
Finite Supply: Precious metals like platinum, palladium, and rhodium are naturally occurring resources that are finite in supply. Recycling these metals conserves them for future generations.
-
Reduced Mining Impact: Recycling reduces the need for new mining operations, which can have significant environmental impacts, such as habitat destruction and pollution.
2. Energy Efficiency:
-
Reduced Manufacturing Costs: Recycled PGMs are often available at lower costs compared to newly mined metals, reducing the energy and resources required for their production.
-
Product Longevity: Products made with recycled PGMs can have a longer lifespan, contributing to overall energy efficiency and reduced waste.
3. Environmental Benefits:
-
Reduced Pollution: Recycling catalytic converters helps prevent the release of harmful pollutants into the environment, improving air quality and protecting ecosystems.
-
Carbon Footprint Reduction: The recycling process itself typically has a lower carbon footprint compared to mining and refining new metals.
4. Economic Advantages:
-
Job Creation: The PGM recycling industry creates jobs and supports local economies, especially in regions with a strong recycling infrastructure.
-
Supply Chain Resilience: A robust recycling industry helps ensure a stable supply of precious metals, reducing dependence on foreign sources and strengthening supply chain resilience.
By choosing to recycle your catalytic converters, you are directly contributing to a more sustainable future. Your actions help conserve natural resources, protect the environment, and support a stronger economy.

Why PGM Recycling Matters
Resource Optimization:
-
Importance: Resource optimization is crucial for conserving natural resources and promoting a circular economy.
-
PPMRCC Contribution: By participating in PPMRCC, individuals can contribute to returning valuable precious metals to industries and promoting sustainability.
Catalytic Converter Precious Metal Content:
-
Historical Trends: Auto manufacturers have used varying concentrations of platinum, palladium, and rhodium in catalytic converters based on environmental regulations. Platinum has traditionally been used in the highest concentration.
-
Recent Changes: Newer catalytic converters are becoming smaller with higher precious metal content, driven by rising platinum prices. This has led to the emergence of new players in the industry.
Overall, the precious metal content in catalytic converters has evolved over time due to changing regulations and market dynamics. Recycling catalytic converters through companies like PPMRCC plays a vital role in resource conservation and promoting a circular economy.
Environmental Impact of PGM Mining:
-
Negative Impacts: Mining PGMs is associated with deforestation, soil degradation, and habitat destruction.
-
Reduced Need for Mining: Recycling catalytic converters helps reduce the demand for new mining activities, thereby minimizing these environmental impacts.
Benefits of PGM Recycling:
-
Resource Conservation: Recycling PGMs conserves precious natural resources.
-
Carbon Footprint Reduction: Recycling also contributes to minimizing the global carbon footprint.
Palladium Trends:
-
Increased Use: Carmakers have increasingly used palladium in catalytic converters due to its lower cost compared to platinum.
-
Misconception: Many suppliers still believe that platinum is the primary metal to consider when selling converters, overlooking the increased use of palladium.
-
Market Reality: Palladium currently represents more than 60% of the metal content in catalytic converters, often exceeding platinum by three times.
Recycling PGMs through catalytic converter recycling plays a significant role in reducing the environmental impact of mining and promoting sustainability. It's essential for suppliers to be aware of the changing trends in precious metal use in catalytic converters to maximize the value of their materials.
Understanding PGM Analysis: XRF and ICP
X-ray Fluorescence (XRF) and Inductive Coupled Plasma (ICP) are two essential technologies used in laboratories to analyze the precious metal content of catalytic converters, specifically platinum, palladium, and rhodium (PGMs).
XRF (X-ray Fluorescence):
-
Principle: XRF works by bombarding the sample with X-rays, which cause the atoms in the sample to emit characteristic X-rays. These emitted X-rays can be used to identify the elements present in the sample and determine their relative concentrations.
-
Advantages: XRF is a relatively rapid and non-destructive technique, making it suitable for initial screening and quality control purposes.
-
Limitations: XRF may not be as accurate as ICP for very low concentrations of elements or for complex matrices.
ICP (Inductive Coupled Plasma):
-
Principle: ICP involves introducing the sample into a high-temperature plasma, which excites the atoms in the sample. The emitted light is then analyzed to determine the concentration of elements.
-
Advantages: ICP offers high sensitivity and accuracy, making it ideal for precise measurements of precious metal content in catalytic converters.
-
Limitations: ICP is generally more time-consuming and requires more sample preparation than XRF.
By using these two technologies, processors can provide a comprehensive assay report that includes:
-
Troy ounce recovery figures: The total amount of PGMs recovered from the catalytic converters.
-
Parts per million (PPMs): The concentration of PGMs in the sample, expressed in parts per million.
-
Metal return percentages: The percentage of PGMs recovered relative to the estimated initial content.
-
Other information: Additional details such as the purity of the recovered PGMs and any impurities present.
This information is crucial for recyclers as it allows them to accurately assess the value of their catalytic converter inventory and make informed decisions regarding pricing and hedging.
Would you like to know more about the specific applications of XRF and ICP in PGM analysis or the challenges associated with these techniques?

1. Assay Analysis:
-
Precious Metal Content: The assay analysis determines the exact quantities of platinum, palladium, and rhodium present in the ceramic powder. This information is crucial for determining the overall value of the converter.
2. Pyrometallurgical Processing:
-
High-Temperature Treatment: The ceramic powder is subjected to high-temperature processes like smelting or fire assaying. These processes separate the precious metals from the base metals and other impurities.
-
Refining: The refined precious metals are further purified to achieve a high-purity grade.
3. Hydrometallurgical Processing:
4. Electrorefining:
-
Purification: Electrorefining is a final purification step where the precious metals are deposited onto a cathode in an electrolytic cell, removing any remaining impurities.
5. Product Formation:
-
Final Products: The purified precious metals are then formed into various products, such as ingots, bars, or powders, depending on the market demand and desired applications.
It's important to note that the specific processing methods and equipment used can vary depending on factors such as the type of catalytic converter, the precious metal content, and the desired purity level.
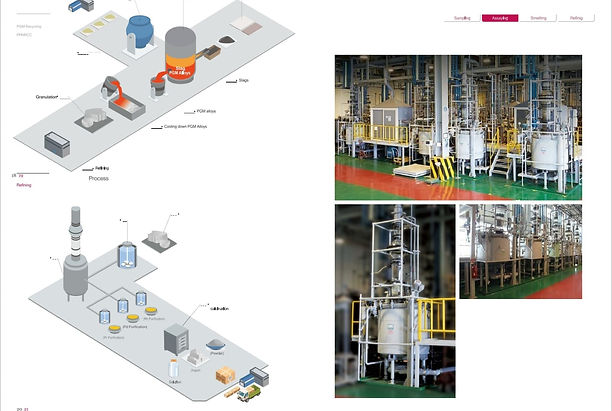
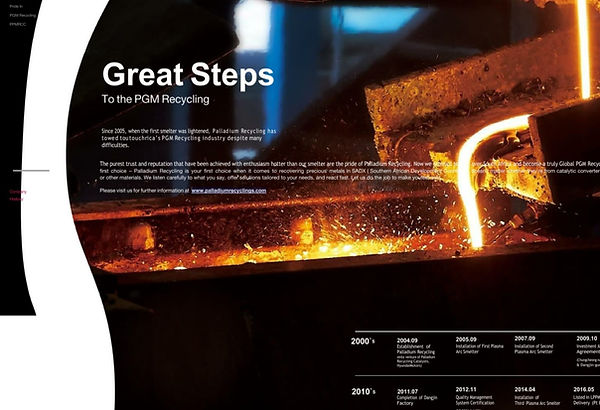
1. Emission Reduction Standards:
-
Stringent Regulations: Governments worldwide have implemented increasingly strict emission standards to combat air pollution. These standards require vehicles to produce fewer harmful gases like nitrogen oxides (NOx), carbon monoxide (CO), and hydrocarbons (HC).
-
Catalytic Converters as a Solution: Catalytic converters, equipped with precious metals like platinum, palladium, and rhodium, act as filters, chemically transforming these harmful gases into less harmful substances.
2. Fuel Efficiency and Emissions:
-
Reduced Fuel Consumption: More fuel-efficient vehicles produce fewer emissions simply because they burn less fuel.
-
Smaller Engines: Smaller engines, often found in hybrid or electric vehicles, consume less fuel and, consequently, emit fewer pollutants.
-
Start-Stop Systems: These systems reduce engine idle time, leading to lower fuel consumption and emissions.
3. Precious Metal Content and Emission Reduction:
-
Increased Demand: As emission standards tighten, the demand for catalytic converters with higher precious metal loadings increases to ensure effective pollutant reduction.
-
Technological Advancements: While higher loadings can be costly, advancements in catalytic converter technology and the development of more efficient precious metal alloys can help mitigate these costs.
4. Challenges for Recyclers:
-
Unknown Loadings: The lack of public information about catalytic converter precious metal content poses a significant challenge for recyclers. They often have to wait for vehicles to reach the end of their lifespan to determine the actual loadings.
-
Market Fluctuations: Variations in precious metal prices can also impact the profitability of recycling catalytic converters.
In conclusion, the pursuit of fuel efficiency and reduced emissions is driving the evolution of catalytic converter technology. As emission standards become more stringent, we can expect to see a continued increase in the demand for catalytic converters with higher precious metal loadings. This, in turn, will influence the recycling industry as recyclers navigate the challenges of unknown loadings and fluctuating market prices.
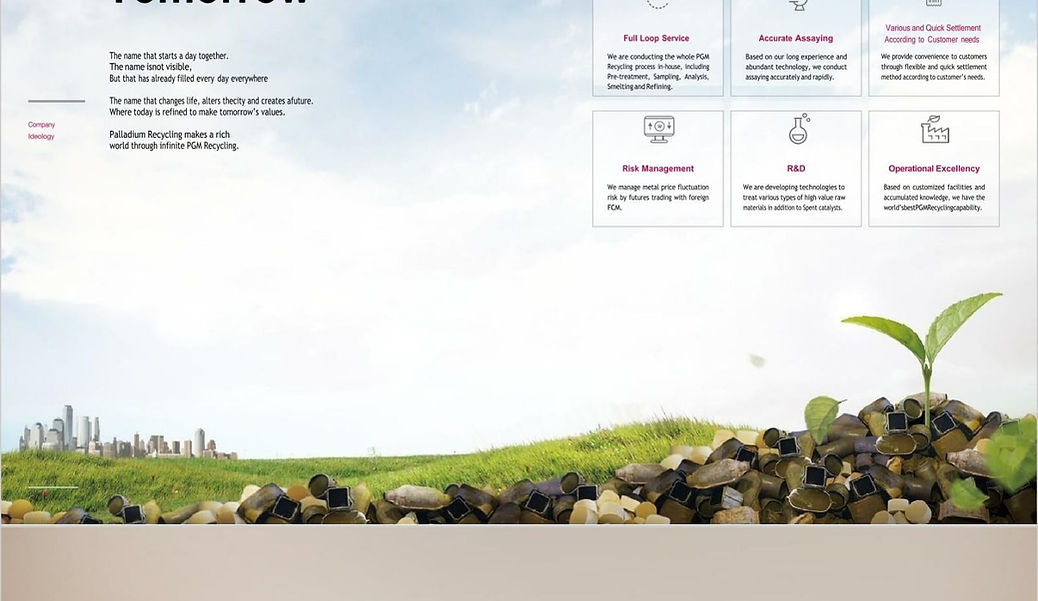
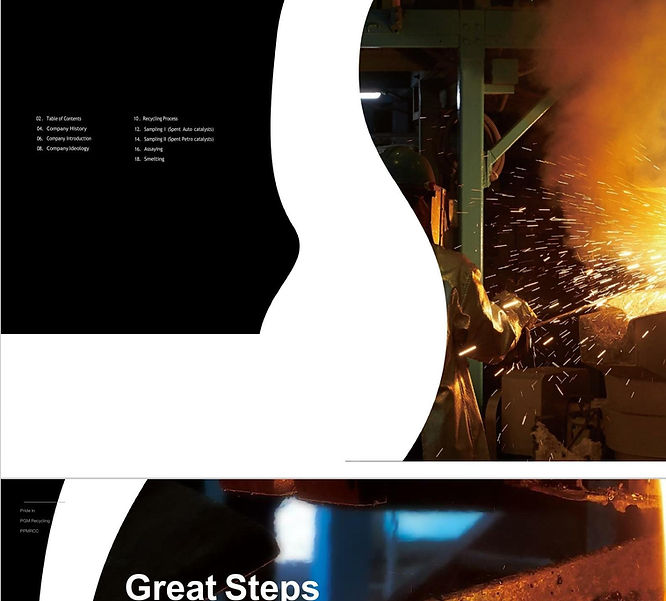


PPMRCC( Palladium Recycling)
-
Experience: Established in 2005, PPMRCC has a strong track record in the catalytic converter scrap business.
-
Growth: The company has expanded its operations to become a leading information provider and toll-refining purchaser in South Africa.
-
Sustainability Focus: PPMRCC is committed to sustainable precious metal recycling and extracting maximum value from catalytic converters.
Why PGM Recycling Matters:
-
Resource Optimization: Recycling PGMs contributes to conserving natural resources and promoting a circular economy.
-
Environmental Impact: Recycling reduces the need for new mining activities, which have significant environmental impacts.
-
Carbon Footprint Reduction: Recycling PGMs helps minimize the global carbon footprint.
Catalytic Converter Precious Metal Content:
-
Historical Trends: Auto manufacturers have used varying concentrations of platinum, palladium, and rhodium in catalytic converters based on regulations.
-
Recent Changes: Newer catalytic converters are becoming smaller with higher precious metal content due to rising platinum prices.
Impact of Emission Reduction Efforts:
-
New Technologies: Carmakers are exploring ways to reduce emissions and improve fuel efficiency, including lighter materials, battery-powered systems, and smaller engines.
-
Converter Changes: These changes may affect catalytic converter precious metal content, but specific information is often not readily available.
Processing Challenges and Solutions:
-
Silicon Carbide Substrates: Newer DPF models with silicon carbide substrates require specific smelting processes and handling.
-
PPMRCC Approach: PPMRCC has developed specialized procedures to handle these substrates accurately and efficiently.
-
Supplier Support: PPMRCC provides guidelines for safe and secure shipping of catalytic converters and offers various services to support suppliers, including fast settlement, photo grading, and educational resources.
Overall, PPMRCC offers a comprehensive range of services for catalytic converter recycling, including accurate valuation, efficient processing, and support for suppliers. The company's focus on sustainability and its expertise in handling different types of catalytic converters make it a valuable partner for those involved in the precious metal recycling industry.
Understanding PGM Analysis: XRF and ICP
X-ray Fluorescence (XRF) and Inductive Coupled Plasma (ICP) are two essential technologies used in laboratories to analyze the precious metal content of catalytic converters, specifically platinum, palladium, and rhodium (PGMs).
XRF (X-ray Fluorescence):
-
Principle: XRF works by bombarding the sample with X-rays, which cause the atoms in the sample to emit characteristic X-rays. These emitted X-rays can be used to identify the elements present in the sample and determine their relative concentrations.
-
Advantages: XRF is a relatively rapid and non-destructive technique, making it suitable for initial screening and quality control purposes.
-
Limitations: XRF may not be as accurate as ICP for very low concentrations of elements or for complex matrices.
ICP (Inductive Coupled Plasma):
-
Principle: ICP involves introducing the sample into a high-temperature plasma, which excites the atoms in the sample. The emitted light is then analyzed to determine the concentration of elements.
-
Advantages: ICP offers high sensitivity and accuracy, making it ideal for precise measurements of precious metal content in catalytic converters.
-
Limitations: ICP is generally more time-consuming and requires more sample preparation than XRF.
By using these two technologies, processors can provide a comprehensive assay report that includes:
-
Troy ounce recovery figures: The total amount of PGMs recovered from the catalytic converters.
-
Parts per million (PPMs): The concentration of PGMs in the sample, expressed in parts per million.
-
Metal return percentages: The percentage of PGMs recovered relative to the estimated initial content.
-
Other information: Additional details such as the purity of the recovered PGMs and any impurities present.
This information is crucial for recyclers as it allows them to accurately assess the value of their catalytic converter inventory and make informed decisions regarding pricing and hedging.
Would you like to know more about the specific applications of XRF and ICP in PGM analysis or the challenges associated with these techniques?
The smelting phase is a critical step in the PGM recycling process, where the extracted precious metals are refined and transformed into a usable form. Here's a breakdown of the process:
-
Arc Furnace: The extracted PGMs are fed into an arc furnace, a high-temperature furnace that uses electric arcs to melt the metals.
-
Chemical Leaching and Separation: Chemical processes are employed to separate the PGMs from other impurities and to refine them to a high purity level. This often involves using strong acids or bases to dissolve unwanted elements.
-
Metal Sponges or Pure Elemental State: The refined PGMs are typically transformed into metal sponges or their pure elemental state. Metal sponges are porous structures that can be further processed or used directly in various applications.
Once the smelting phase is complete, the resulting PGMs are considered physical ounces and are ready to re-enter the global market. These precious metals can be purchased, resold, or traded for various purposes, including jewelry, industrial applications, and investments.
